Ⅰ.Notes:
At present,the laboratory commonly used water-heated reactor is divided into PTFE and PPL two kinds of liner, shell material is divided into 304 stainless steel and 316 stainless steel, due to the difference between good and bad materials often different materials have different service life, PTFE material when working outside the heating temperature is recommended not to exceed 230 ℃, PPL material is recommended not to exceed 260 ℃, and the heating rate is recommended ≤ 5 ℃ / min, can be used. When the reaction is completed, the kettle should be cooled naturally to room temperature before opening the lid, *Note that the kettle should be cooled naturally to room temperature before opening the lid. Never disassemble under pressure. The normal kettle liner should not be filled with more than 70% of the total kettle volume. Explosion-proof kettles should also be filled to no more than 80%. The hydrothermal reactor is normally designed for a pressure of 3.0 MPa. Make sure that the maximum value of the mixed vapour pressure generated by the reaction system at the reaction temperature is below 3.0 MPa before use. The hydrothermal kettle does not have an overpressure relief device and should not be used at excessive temperatures or pressures to avoid danger. As the inner liner of the kettle is made of Teflon or PPL, both of which are high molecular plastics, the lid should not be tightened too tightly when first used to avoid deformation caused by the heat rise and squeeze of the liner at high temperatures.
The use of hydrothermal Synthesis Reactor is not recommended for reactions with the following characteristics (below).
1. The boiling point of the solvent is below 60°C (e.g. ether, acetone, dichloromethane, etc.)
2. A large amount of gas is generated during the reaction.
3. The material has flammable or explosive properties or is volatile in toxicity and the degree is extremely highly hazardous
4. The duration of the reaction exceeds 100 h and the temperature is always above 250°C.
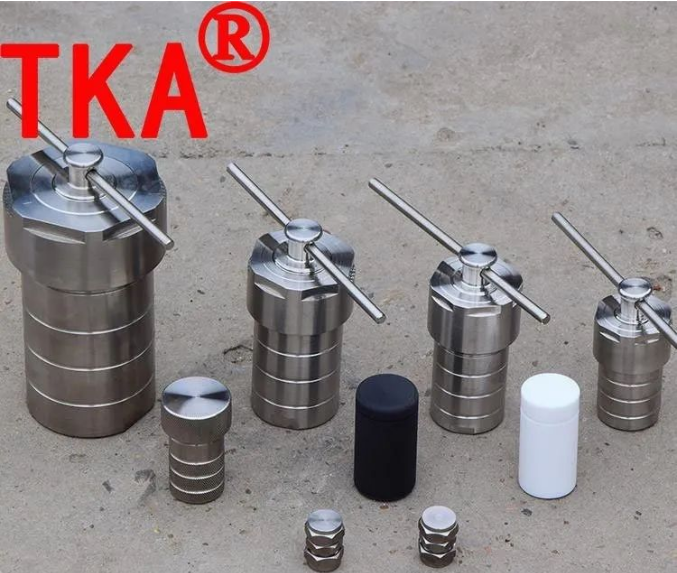
The image of the Hydrothermal Synthesis Reactor for PPL and PTFE lined.
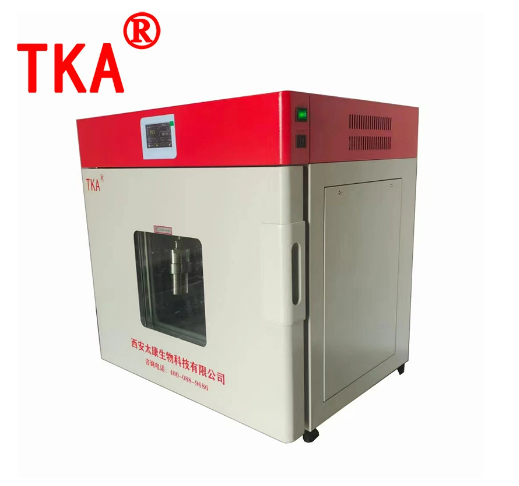
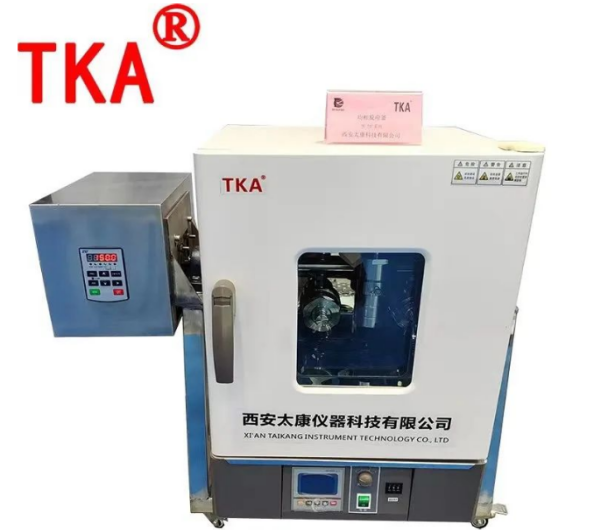
The image of Multi-combination Rotary type Hydrothermal Synthesis Reactor
Ⅱ:Safe Operation.
1. Pour the reactant into the PTFE bushing or PPL bushing and ensure that the dosing factor is less than 0.8.
2. Ensure that the lower gasket of the kettle is correctly positioned, then put in the PTFE or PPL bushing and upper gasket, tighten the kettle lid first, then screw the kettle lid until it is twisted and tightened with a screw.
3、Place the hydrothermal synthesis reactor in the heater and raise the temperature to the required reaction temperature according to the prescribed heating rate.
4. When confirming that the temperature inside the belly is lower than the boiling point of the solvent of the reactant species, the lid of the kettle can only be opened for subsequent operation. When the reaction is finished and the temperature is cooled down, it should also be operated in strict accordance with the specified cooling rate to help prolong the service life of the reactor.
5. After confirming that the temperature inside the kettle has cooled down to its natural temperature, first loosen the kettle lid by twisting it with a screw, then open the lid.
6. Clean the kettle in time after each use to avoid rust and corrosion. Take extra care to clean the kettle body and lid line seals and prevent them from being damaged by bruising.
Ⅲ:Reactor Cleaning.
1. When cleaning the hydrothermal reactor for the first time, slightly add some alkali or water to the liner and boil it for some time. When using the hydrothermal reactor for the first time, make sure not to heat it quickly, but to slowly program the heating up nor make the temperature too high, otherwise the PTFE lined will be easily deformed. Start at 150°C for a few hours respectively, then hold at 200°C for a few more hours, after which remove and cool naturally. Afterwards the experiment is carried out again at a temperature of 200 degrees Celsius when the liner of the hydrothermal reactor does not appear to be deformed.
2、The reaction medium of the hydrothermal synthesis reactor is different, the cleaning method is also different.If it is a silicon system, you can add some hydrofluoric acid or alkali to heat and wash it after use; if it is a silicon metal system, it depends on what acid it is dissolved in, and hydrochloric acid needs to use aqua regia: concentrated nitric acid and concentrated hydrochloric acid (three to one ratio). For example: use potassium permanganate dissolved in water, then add 3-5mL of concentrated hydrochloric acid, put it into the reaction kettle and seal it well, 180 degrees of hydrothermal reaction for 5-10 hours, so that the washed out reaction liner is clean inside and out.
3. Cleaning methods: such as aqua regia: concentrated nitric acid and concentrated hydrochloric acid three to one ratio: at the end of the experimental reaction, add about 1:5 nitric acid and water in the hydrothermal reaction kettle mixed solution, and then heated to 180 degrees Celsius for about 12 hours, these data are not fixed, need to be based on the specifics of your experimental reaction, the ratio of mixed solution is not necessarily 1:5, the temperature is not necessarily to 180 The ratio of the mixture may not necessarily be 1:5 and the temperature may not necessarily be 180°C. Here is a reference figure for you. However, there is a drawback to this method, which is that it makes the experiment less reproducible. The oxalic acid solution is boiled for 6 hours at a temperature of 160 degrees depending on the experiment.
Ⅳ:Reactor testing for gas leaks
When doing hydrothermal reactions in the laboratory, we find that the hydrothermal synthesis reactor has a gas leak no matter how many times we do it, how should we find out where it leaks in the face of a hydrothermal synthesis reactor?
The hydrothermal synthesis reactor generally ranges from a dozen millilitres to several hundred litres in volume. To check the location of air leakage from the hydrothermal synthesis reactor, you can first apply pressure and then listen to the sound of air leakage, this applies to the more obvious ones, in most cases, the reactor leakage is not audible, this method is only applicable in a few cases.
Secondly, you can use a dropper to drip water from the various links in the reactor to see if bubbles are produced. This method is time consuming and requires careful observation. It is suitable for those who have a rough idea of a leak or who have already replaced a leaky part and need to check again whether the leak has been corrected.
The most straightforward and simple method is to prepare a large container, fill it with water and then immerse the reactor completely in the water to see which part of the reactor has bubbles coming out. After picking up the leaks, blow dry the reactor with a hot air blower or wipe it dry.
Post time: Jan-11-2023